Os automóbiles modernos pouco teñen que ver con aqueles que se fabricaban a principios do século XX, e da mesma maneira cambiou o mercado: se antes un mesmo modelo podía fabricarse durante décadas sen apenas cambios, na actualidade rexen a innovación e as modas. E, neste marco de continua transformación, a colaboración entre socios tecnolóxicos cobra unha gran importancia, como no caso de Matrici, Quantech ATZ, a Sociedade Fraunhofer e mais o CESGA, unidos nun mesmo proxecto dentro do programa europeo Fortissimo.
Matrici é unha empresa integrada na División de Conformado e Ensamblaxe, dentro da área Industrial da cooperativa vasca Grupo Mondragón, e dedícase principalmente á fabricación por estampación en metal de pezas exteriores de carrocería e reforzos para o sector automobilístico, en tanto que Quantech ATZ é responsable do desenvolvemento e adaptación do software Stampack, específico para o cálculo polo método de elementos finitos dese tipo de pezas. Pola súa banda, o Fraunhofer Institute for Algorithms and Scientific Computing SCAI, de Alemaña, actuou como servidor de licenzas de software, mentres que o CESGA achegou a capacidade de executar HPC, isto é, High Performance Computing ou Computación de Alto Rendemento, cos seus supercomputadores e redes de computación distribuída.
Actualmente, Matrici está a desenvolver os procesos necesarios para traballar con aluminio e con aceiros convencionais de alta resistencia (HSS), que permiten unha produción a menor custo de vehículos máis lixeiros, axudando os fabricantes a adaptarse ás esixentes normativas de emisións e ó desenvolvemento do coche eléctrico. Tamén nos últimos anos, no sector do automóbil están a producirse importantes cambios en termos de requisitos para os novos modelos, con máis probas de choque de seguridade, pero con menos peso, para lograr unha redución de consumo, e por tanto menos contaminación. É por iso que, para cumprir con estas esixencias, estanse a incorporar novos materiais, porque as súas boas cualidades poden axudar a reducir os espesores en distintas partes do chasis, como os piares ou os reforzos laterais.
A alta resistencia característica dos aceiros HSS fai factible o desenvolvemento de deseños eficientes en termos de masa, o que aforra consumo de combustible, ó mesmo tempo que xera maior resistencia a impactos en colisións. A diferenza de moitos outros materiais, este aceiro pode alcanzar esas metas sen causar un aumento no custo total para o fabricante, pero a alta resistencia deste material implica o uso dunha maior presión durante o proceso de estampación e, en xeral, isto aumenta a dificultade de todo o proceso. Entre os principais problemas asociados da incorporación de aceiros HSS ou de aluminio están o severo desgaste das ferramentas de conformado e mesmo a ruptura prematura despois de facer poucas pezas. Outro problema importante do emprego dos novos materiais é a forte recuperación elástica despois da conformación (efecto de resorte), xerada polo alto límite de elasticidade destes materiais.
O traballo de Matrici abarca todo o desenvolvemento conceptual das pezas, o seu deseño, a súa fabricación e mesmo a adaptación das plantas de ensamblaxe onde logo se combinarán con outras para formar un vehículo completo, e, evidentemente, nese proceso existen importantes requirimentos en canto a aspecto, xeometría e comportamento do compoñente. Ricardo Muguerza, responsable do proxecto en Matrici, indica que “a precisión no cálculo de elementos finitos está a aumentar nos últimos anos, incluíndo algoritmos mellorados e novas variables baseadas na aparición de novos materiais e no coñecemento exacto do proceso. Aínda hoxe estanse introducindo novos conceptos para o cálculo, que requiren varios días para un proceso completo de varias operacións. Debido ó gran número de ciclos requiridos para obter unha simulación satisfactoria, desde a industria estamos a requirir solucións que poidan abordar o tempo de cálculo en horas en lugar de días. Para lograr estes requisitos, é necesario o uso dunha enorme capacidade de CPU, na primeira etapa da enxeñería”. Por iso, engade, “o que pretendiamos pola parte cliente era executar os cálculos cun software de moita precisión no menor tempo posible, porque iso implica que o produto terminado sae antes ó mercado: o beneficio para nós é o ‘time-to-market’, o facelo o máis rapidamente posible, coa maior precisión e calidade, para así anticiparnos ó mercado”, algo que resulta imprescindible para prosperar no complicado panorama da economía global actual.
Para acelerar todo o proceso, explícanos Ricardo Muguerza que desde a súa empresa buscaron “unha aplicación de cálculo numérico de sólidos, para o conformado profundo de pezas de materiais avanzados de automoción, o que é a ‘pel’ ou revestimento exterior (portas, capó, teito, aletas…), en aceiros e aluminio, e partes estruturais como reforzos de automoción en aceiros de alto límite elástico HSS”. Esa aplicación era a que proporcionaba Quantech ATZ, un ‘software vendor’ establecido en Barcelona que desenvolve programas para a súa utilización no campo do estampado de metal, ou, en palabras de Fernando Rastellini, o seu director técnico, “o que nós ofrecemos ás empresas é facer unha simulación virtual do proceso, só importando coñecementos da xeometría das ferramentas, definindo o material (a chapa de aceiro que estou a utilizar), e algún máis dos parámetros do proceso, como a forza da prensa, para poder obter unha solución polo método de elementos finitos, dunha maneira rápida e sinxela, e por suposto, ofrecendo uns resultados o máis aproximados posible ó proceso real”.
Pero ademais, para satisfacer as necesidades de Matrici necesitábase tamén a elaboración dun software de paralelización, porque, como lembra o seu responsable de proxecto, “na industria temos a limitación do número de CPUs (Central Processing Units ou procesadores) que hai en cada estación de traballo, e o programa de cálculo numérico que desenvolve e comercializa Quantech está baseado en sólidos e require de moito tempo de computación para ser lanzado a un só procesador”. A solución pasaba por tanto pola colaboración cunha institución que puidese achegar altas capacidades de cálculo, e aí, sinala Ricardo Muguerza, entraría o CESGA: “dentro da empresa podemos lanzar a oito procesadores, pero aínda así os tempos de cálculo son moi elevados, e concretamente, no prototipo en que estivemos traballando, o tempo de cálculo era de vinte e catro horas lanzado sobre unha estación de traballo a oito procesadores, e co mesmo prototipo que lanzamos no CESGA cunha capacidade próxima a 2.000 procesadores, reducimos o tempo de cálculo un 91%, de vinte e catro horas a dúas”.
Ademais, agrega Muguerza, a simulación numérica permite aforrar tempo doutra maneira: “antes facíanse os prototipos primeiro, para ver se resistían as probas de ensaio físico, e agora facémolo ó revés, primeiro faise a fase de cálculo de factibilidade de peza, para comprobar se é posible ou non, e logo realízase a peza, de modo que nos anticipamos ós tests finais e comprobamos se o produto é factible antes de que sexa fabricado fisicamente”. Noutro sentido, a anticipación tamén é, de feito, un dos obxectivos de calquera proxecto de I+D+i, ou sexa, Investigación, Desenvolvemento e Innovación, claves para manter o liderado das empresas europeas na economía globalizada do noso tempo, e respecto diso manifesta Ricardo Muguerza que “estamos asombrados moi positivamente da resposta técnica e humana do equipo que participou neste proxecto europeo”, opinión que comparte Fernando Rastellini, quen declara que “participamos en varios proxectos europeos, e seguiriamos colaborando; o que é o I+D, potenciado polas axudas europeas é máis fácil, porque se non ás empresas cústalles investir.
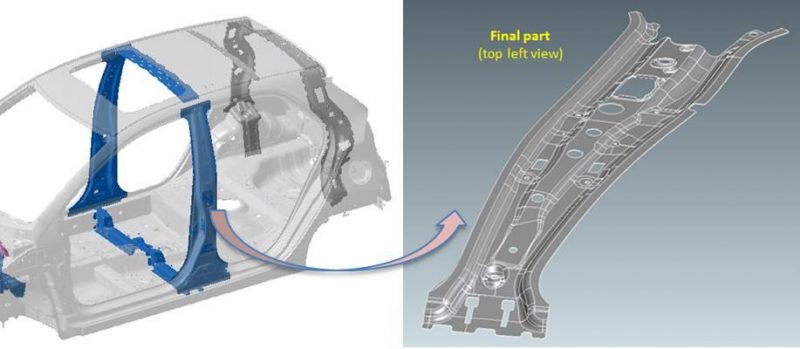
Pilar B dun vehículo, unha das pezas fabricadas en Matrici
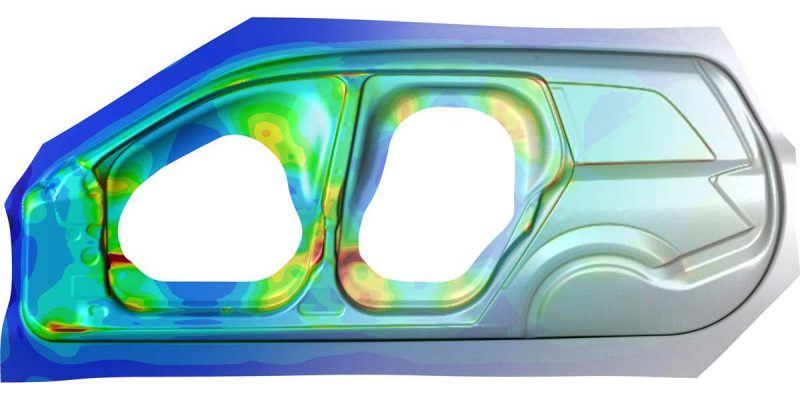
Simulación virtual previa á fabricación dos prototipos Quantech ATZ